Types Of Cardboard Used In The Packaging Industry
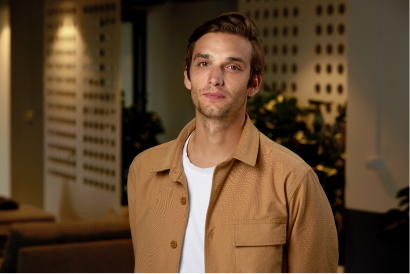
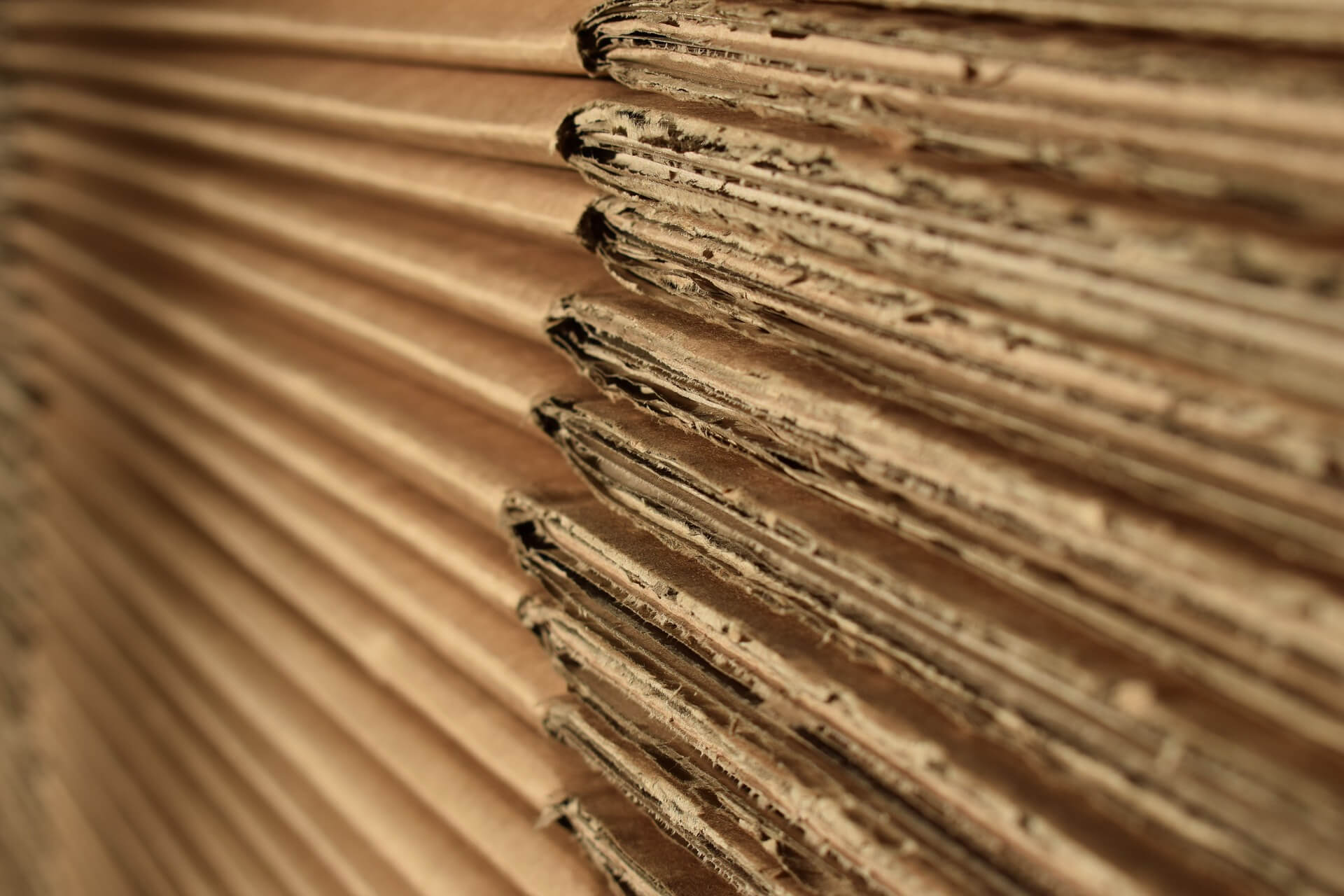
Subscribe now! Receive 15% discount.
Don’t miss out – get 15% off your first order when you join the newsletter. It’s fast, free, and kinda smart.
You're now subscribed!
In this article:
There are many different types of cardboard on the market, owing to the variety of ways that we can use it in everyday life.
With different thicknesses, shapes and forms, cardboard can be an incredibly strong yet lightweight material and even have solid thermodynamic properties.
This article will look at the most common types of cardboard used in common types of packaging in the industry.
It'll also explain why they're so relied upon.
Let's start by looking at what exactly cardboard is made out of.
Types of Paper
Before diving into the various cardboard types, it's essential to know what types of paper or paper pulp are used to make cardboard. These types of paper create different cardboard properties and dictate how we can use the cardboard.
Even with its various uses, there are only really two 'types' of paper used to make cardboard: Kraft and Test liners.
Kraft paper is generally made with virgin softwood trees like pine, spruce and fir.
Virgin means that the fibres in the paper pulp are fresh and haven't been recycled from something else.
The virgin nature of these wood fibres as well as the manufacturing process it requires makes Kraft paper incredibly strong and the easiest type of cardboard to print on.
These reasons make kraft paper the most common type of paper used on cardboard surfaces that will be printed and parts that require structural integrity.
The name 'test' paper doesn't do it justice. It simply means that it's paper that's recycled.
However, as the wood fibres have been damaged in turning it from another paper product into a pulp and then back into cardboard, it's not as strong or easy to print on.
This makes it less costly but sees it primarily used on surfaces that won't be seen.
Both Kraft and test liners are usually made of two laminated layers.
The base layer is used for strength, with the cover layer being of better quality, used for printing and visual appeal.
Test and Kraft liners are the most popular and widely used forms of liners, but others can be used for base and cover layers.
These include variants that sacrifice visual appeal for strength, are bleached white or made from more or less recycled content.
Cardboard types & material construction
Now it's time to look at how cardboard is formed - more specifically, corrugated cardboard, the most common type of cardboard.
In the simplest terms, corrugated cardboard is made from three different elements - a wavy/fluted/corrugated sheet of cardboard between two other flat layers of cardboard.
Each side of the fluted cardboard is glued and attached to the flat layers, and it's the fluted layer that gives corrugated cardboard its strength.
Weights & thicknesses (GSM)
Next in line is how thick these papers are, as it's evident that the paper thickness has a significant impact on the strength of the cardboard.
The Grams per Square Meter (GSM) measurement is the standard way of explaining how thick and heavy the paper is.
You often see cardboard grammage explained like '135/155K'. This means that the inner liner is 135 GSM and the outer liner is 155GSM, with the K on the end indicating a kraft liner.
Wall Types
Wall types are important when you're talking about the types of cardboard used in packaging - and if you're paying such close attention to cardboard, you've probably got some vested interest in packaging!
When the two flat surfaces and the fluted layer of cardboard all combine to create a box, this is generally called a 'single-walled' box because there's a single wall of cardboard.
Below is a 'single wall'
However, you can add another fluting layer and another liner to this existing wall and create a double-walled box.
This type of packaging is a go-to solution for large or heavy items or even delicate items that need extra protection during the shipping process.
Below you can see EB fluted cardboard stack on top of each other.
Automotive and industrial parts that are even heavier can find adequate protection in triple-walled or tri-wall packaging.
Cardboard can be layered inside a box to also improve it's thermal properties, such as keeping the contents cool or warm.
Learn more about Psi Bufet and their thermally insulated packaging here.
Flutes
Flutes are the 'wavy' part of the cardboard. This flute has so much of a bearing on the structural integrity of the cardboard and therefore defines what it can and can't be used for.
Unsurprisingly, it's the fluting that is also a significant contributor to the weight and, consequently, the cost of the cardboard.
By changing the corrugation's height and, therefore, the flutes' size, the cardboard takes on entirely new properties.
There are standardised sizes for fluting that range from E (very fine), which is suited for retail packaging and ideal to be printed onto, right through to A or B flute, which is thick and usually suited to heavy-duty tertiary packaging.
Standardised sizes include:
- A flute: 5mm in thickness
- B flute: 3mm
- C flute: 4mm
- E flute: 1.5mm
- F flute:.2mm
- G flute: 0.5mm
What's the difference between E and B flutes?
The thickness. B flute is thicker, heavier, and therefore stronger.
As you read earlier, cardboard can be double or triple-walled and therefore have an EB flute or a BC flute.
Such combinations are ideal for combining structural security (B flute) with a perfect blank canvas to print onto (E flute).
Popular fluting for double-walled cardboard includes:
- BC flute: 6mm - B + C flutes
- EB flute: 4.5mm - E + B flutes
- AC flute: 8mm - A + C flutes
Corrugated board explanation
With everything you've just learned, you can condense a lot of specific information into a short abbreviation.
Take, for example:
125K/E/125T
This means that the outer layer is 125 gsm Kraft paper, the flute is an E grade, and the inner liner is a 125GSM Test paper.
It's important to remember that the first instance in this sequence is always the external layer.
In the above example, you'd have a 330 gsm kraft paper liner, a C grade flute, and a 220 gsm test paper liner on the inside.
Individual flute uses/info
As you read earlier, there are a lot of standardised sizes in the cardboard industry, especially fluting. Here are some examples of how those fluting sizes are used.
Note: Flute sizing isn't sequential. C flute is thicker than B flute, but E flute is thinner than C. A flute is thicker than C.
B flute
The most common flute used in cardboard boxes, B flute, is the go-to type of cardboard for mailer boxes.
C flute
C flute is between 3.5mm and 4mm in thickness, a little thicker than usual and offers better crash protection than B flute. For this reason, it's commonly used in standard moving and shipping boxes as secondary or tertiary packaging. It's great for stacking but will give out quickly once it's reached its capacity.
E flute
E flute is the thinnest type of corrugated cardboard that's produced in bulk. Between 1mm and 1./5mm in thickness, it provides good crush protection, which also is the ideal form of corrugated cardboard to print on.
BC flute
A common type of double-walled cardboard that's approximately 7mm in thickness. A standard solution used in shipping boxes for heavy products and products that require an extra level of protection.
EB flute
The best of both worlds - a thick and a thin flute.
Between 4mm and 5mm in overall thickness, this setup provides a fantastic surface to print on and strength and durability.
Conclusion
Understanding the role cardboard plays in packaging is vital to making the right decisions in packaging design.
If you're trying to source reliable cardboard packaging, reach out to the team at Packhelp and tell us about the challenge in front of you.